Automated Manhole Printing: A Smarter Way to Shape Flow Profiles
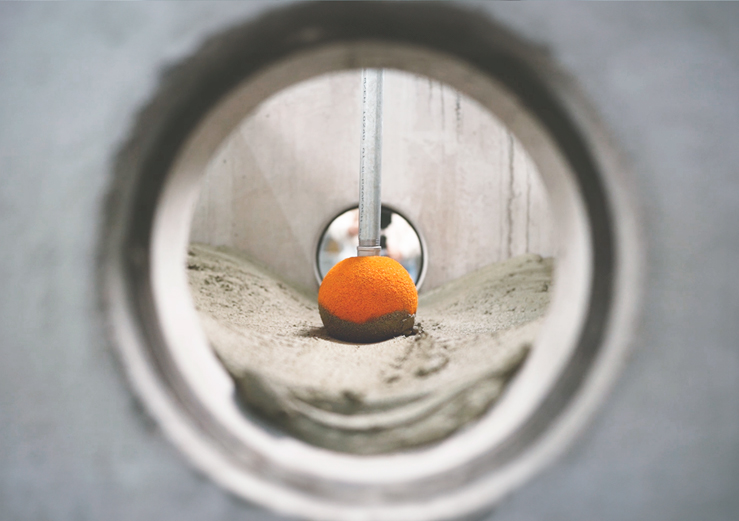
Why Custom Manhole Profiles Are Still Made by Hand
In the Netherlands alone, over 50,000 manholes are produced each year — and around 10% require custom flow profiles.
These profiles are currently shaped manually, making the process:
- Physically demanding
- Time-consuming
- Hazardous to workers
And as expected, there’s a growing shortage of people willing to take on such a difficult task.
Introducing Robotic 3D Concrete Printing for Manhole Interiors
Together with Summum Engineering and IRS Robotics, we developed a safer, scalable alternative:
robotically printed custom manhole profiles inside existing precast pits. Using advanced motion control and material logic, our robots layer concrete with high precision — directly into the base of each manhole.
This eliminates the need for:
- Human access into tight, unsafe spaces
- Manual shaping and smoothing of complex geometries
- Time-consuming finishing work
How It Works: Parametric Design Meets On-Pit Printing
This system is powered by our parametric digital tool, which:
- Adapts in real time to different pit sizes and pipe locations
- Outputs custom toolpaths to the robot
- Ensures smooth, functional flow every time
No rework. No guesswork. Just plug in the specs and print.
This workflow is part of our full setup — from digital input to robotic execution. Explore how to build your own 3D concrete printer setup and start automating smarter.
The Bigger Picture: Scaling Smart Infrastructure
This method bridges the gap between:
- Traditional precast methods (fast, cheap)
- And fully printed components (flexible but slower)
Instead of reinventing the entire system, we enhance what already works — adding smart automation where it matters most.
With this, we move toward safer jobs, better infrastructure, and more sustainable construction.
Dive Into the New Era of Design with Vertico
Discover Vertico's state-of-the-art concrete 3D printing solutions that turn visionary ideas into reality.
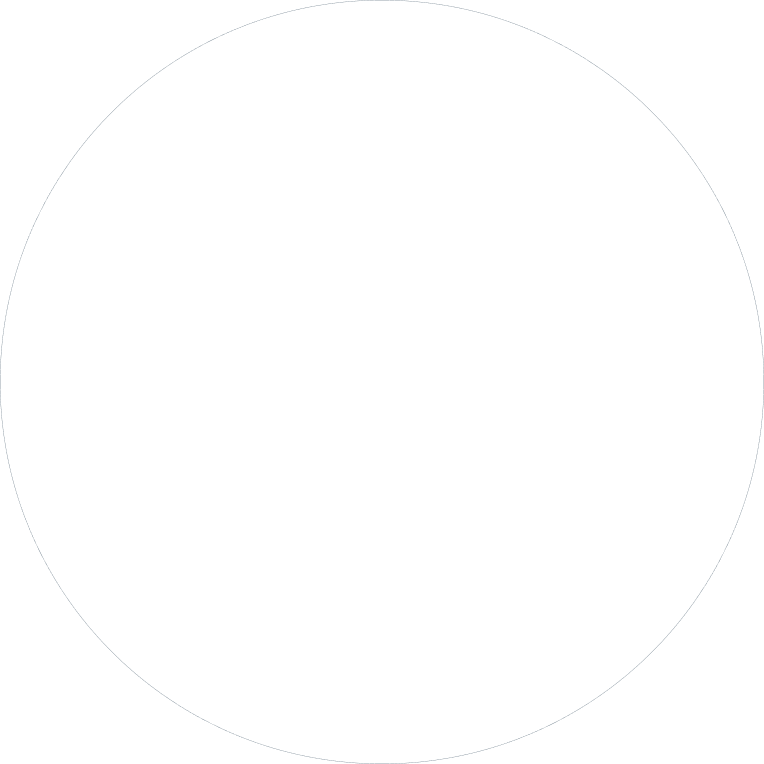
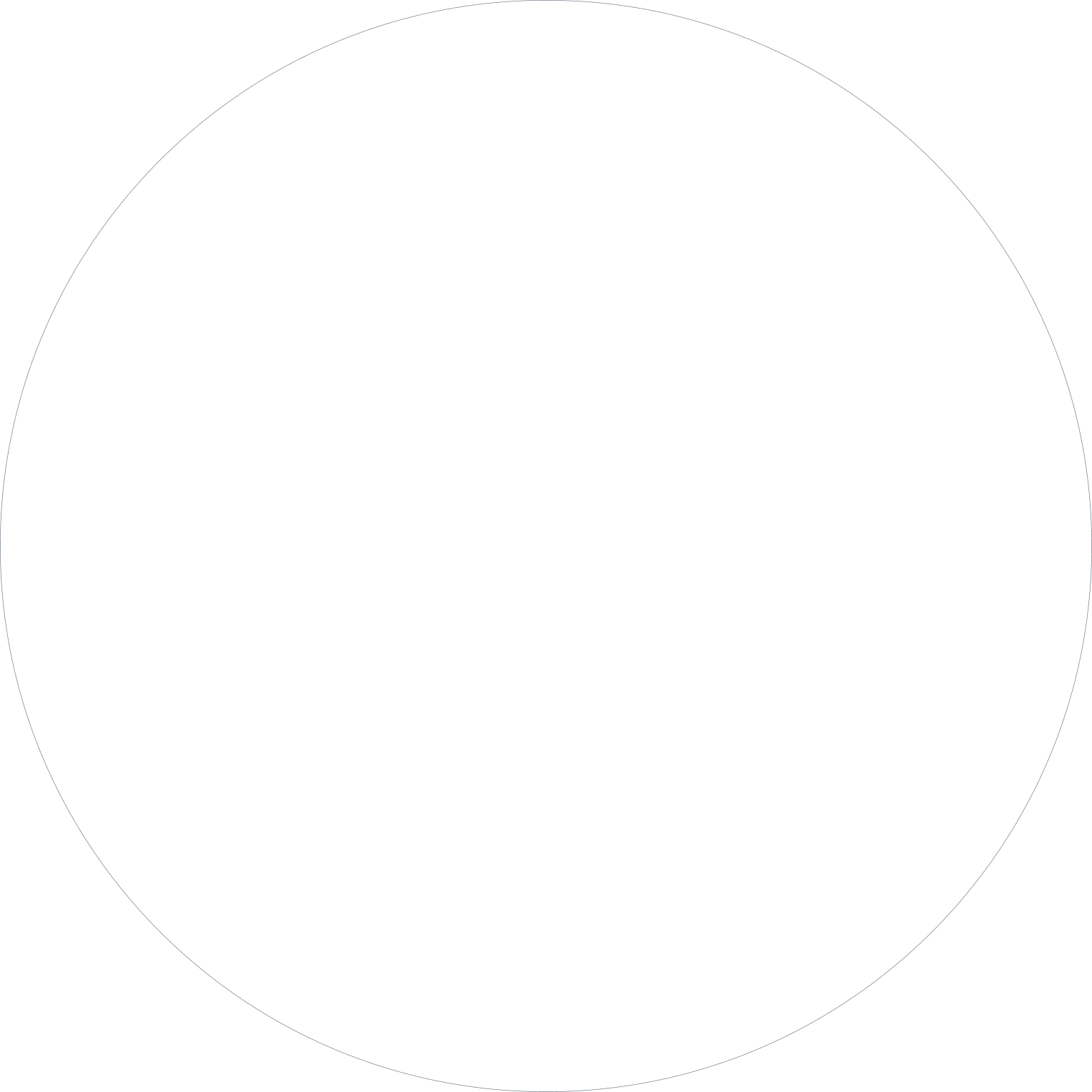