Printing on Mars for the European Space Agency and TUDelft

The Technical Univeristy Delft (TU Delft) and the European Space Agency (ESA) have partnered with Vertico to use its cutting-edge technology to print future underground habitats on Mars. The subsurface structures are part of a project led by Associate Professor and Leader of Robotic Building Henriette Bier at the TU Delft and funded by the ESA.
For extraterrestrial structures to be built above the surface on Mars, their walls must be several meters thick to protect habitants from radiation. TU Delft’s project proposes excavating the ground to create subsurface habitats that are radiation-safe and thermally insulated. The excavated material will be mixed with liquid sulfur to create concrete, which will then be 3D printed to build habitable structures in the excavated areas. Vertico will be using its slicing and robotic printing technology and expertise to translate the optimized geometry of the structures created by TU Delft into printable prototypes.
3D concrete printing technology builds structures by depositing a concrete mixture layer upon layer. This allows for great form freedom and flexibility helps optimize for the most efficient use of material. This optimization often results in unique and organic shapes. These forms are usually costly to build with traditional techniques; however, the robots used in 3D printed produce unique elements with no increase in costs. TU Delft hopes to harness this technology and utilize naturally occurring materials found on Mars to construct their habitats.
This project also demonstrates the possibilities of Vertico’s unique 3D concrete printing techniques. The advantages of 3D concrete printing are being increasingly recognized and desired for a broad range of projects. The need for material & CO2 reduction, automation, and cost-effective production requirements make 3D concrete printing a high-potential innovation.
Related Articles
Dive Into the New Era of Design with Vertico
Discover Vertico's state-of-the-art concrete 3D printing solutions that turn visionary ideas into reality.
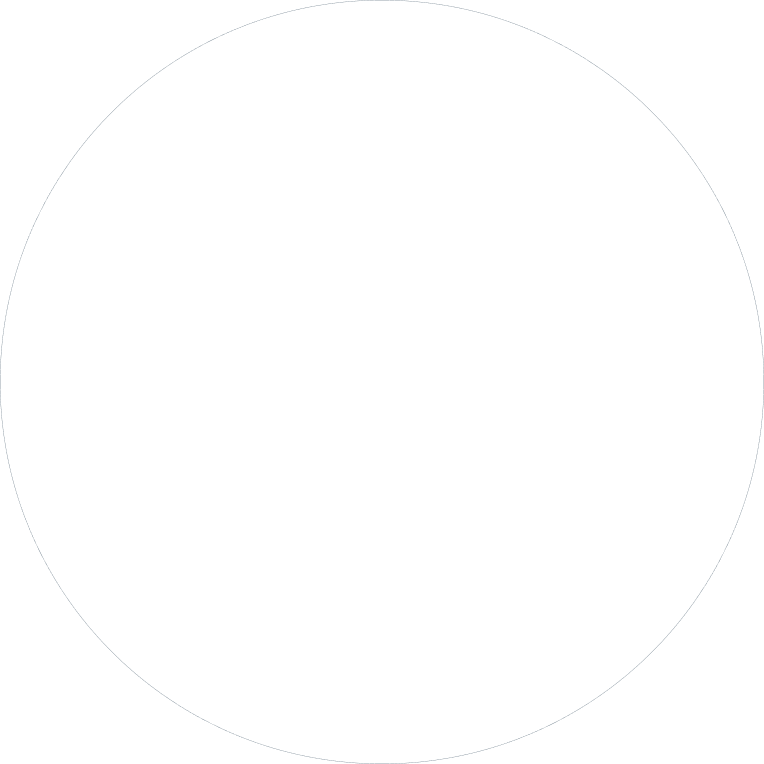
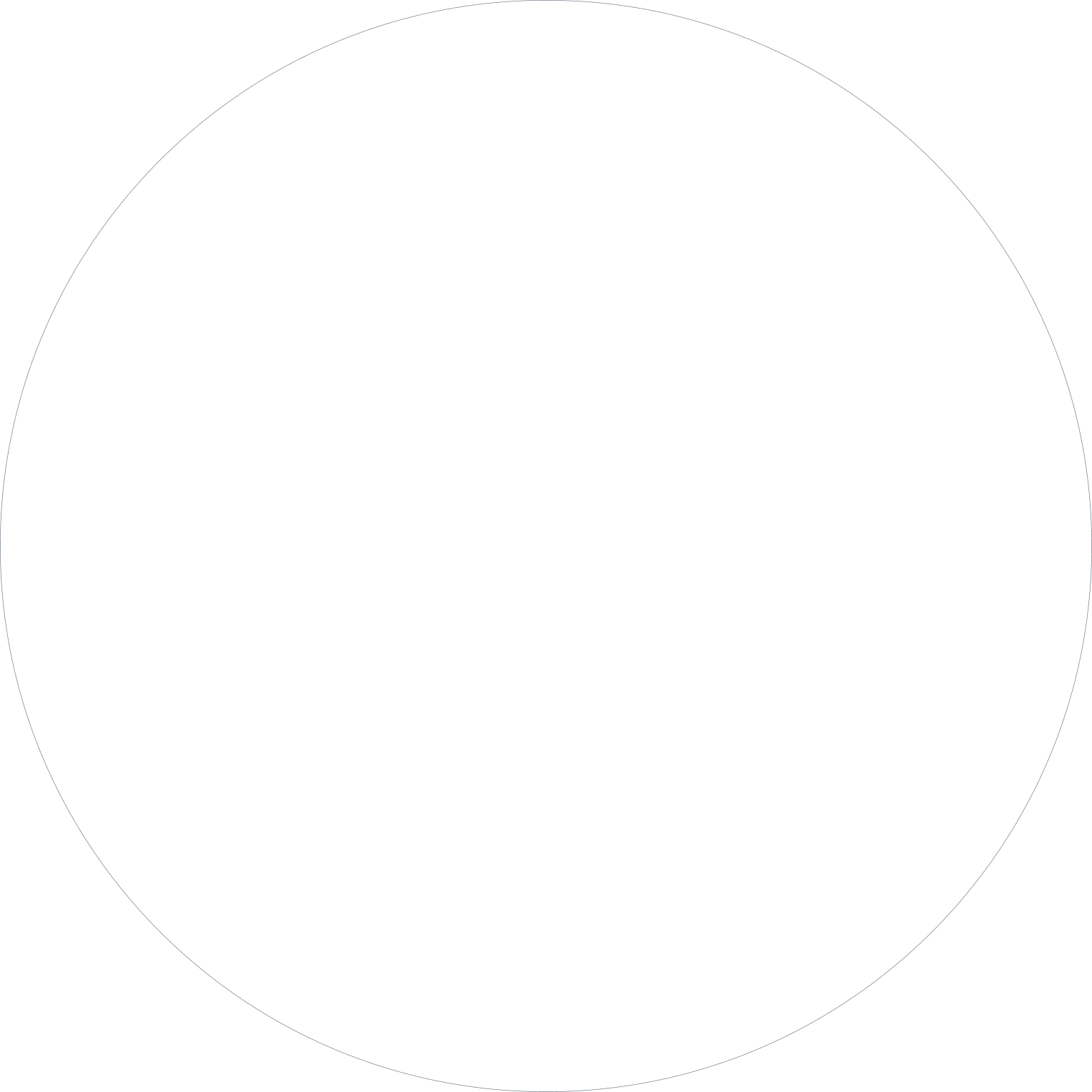