How Can 3D Concrete Printing Enhance Design Possibilities?
At Vertico, we have a collection of outdoor flower pots called "Monje," available in various patterns, sizes, and colors. This demonstrates the vast potential of 3D concrete printing, where even the most bold designs can come to life. Parametric design starts in Rhino + Grasshopper, where we create the shapes and enrich them with patterns or minimalist 3D printed layers. The mathematical equations behind these designs lead to beautiful, intricate forms.
Below, you'll find images of our flower pot collection, each depicted in different contexts, showcasing how versatile our designs can be in public spaces.
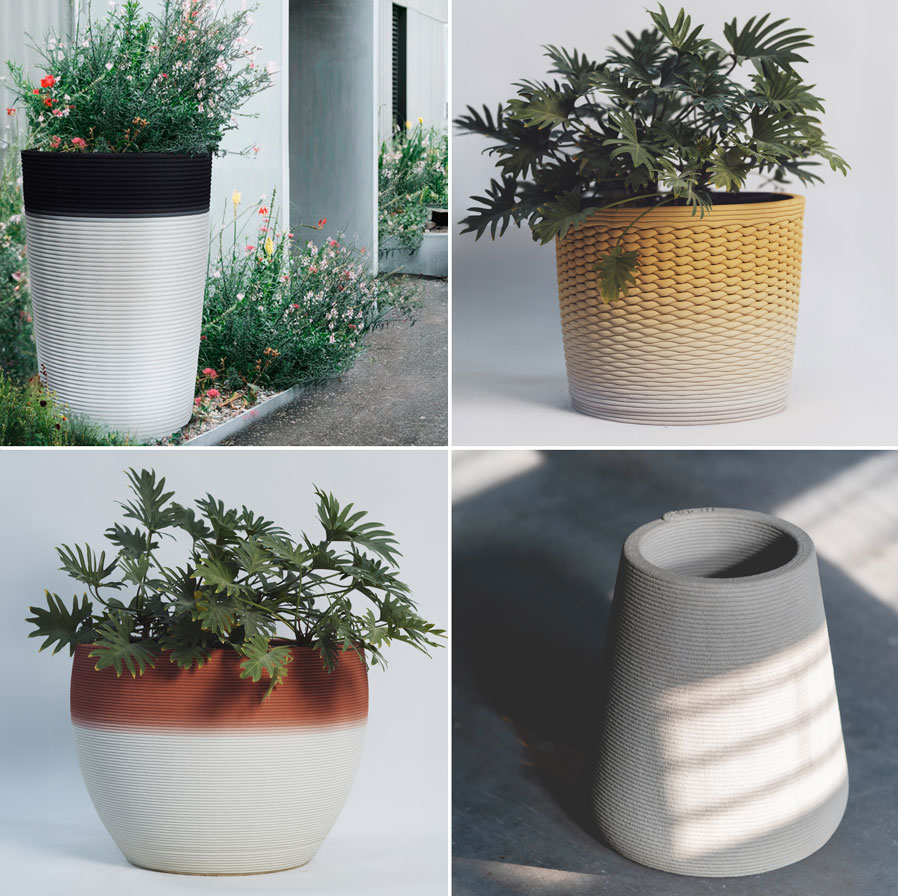
What Makes Color Gradient a Unique Feature in Our Designs?
One of the most exciting features of 3D concrete printing is the ability to introduce color gradients directly into the design. This opens up a whole new level of aesthetic potential, allowing for beautiful, seamless color transitions that can make any structure stand out. At Vertico, we’ve developed a color station that allows us to control the pigment injection process with precision, creating smooth, gradual transitions between colors. This method not only adds a vibrant visual appeal to our pieces but also offers the flexibility to create dynamic color patterns that would be difficult or impossible to achieve with traditional concrete techniques.
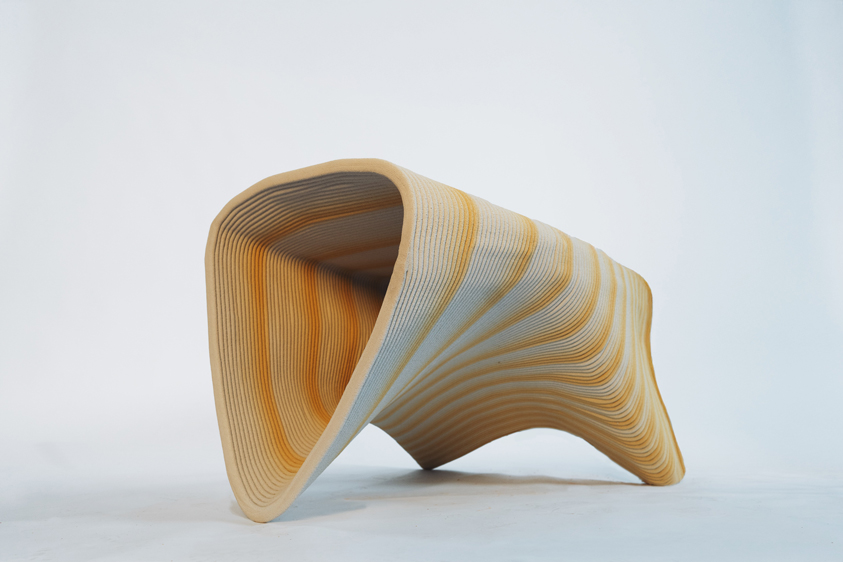
Our latest experiments focus on refining this process even further, pushing the boundaries of color control to achieve even more fluid and consistent gradients. In the striped bench featured in our recent designs, each stripe represents a different speed of color injection, creating a unique and eye-catching effect. This ability to create customized color patterns means that our designs can be fully tailored to the surrounding environment, blending seamlessly into any space or standing out as a bold statement piece.
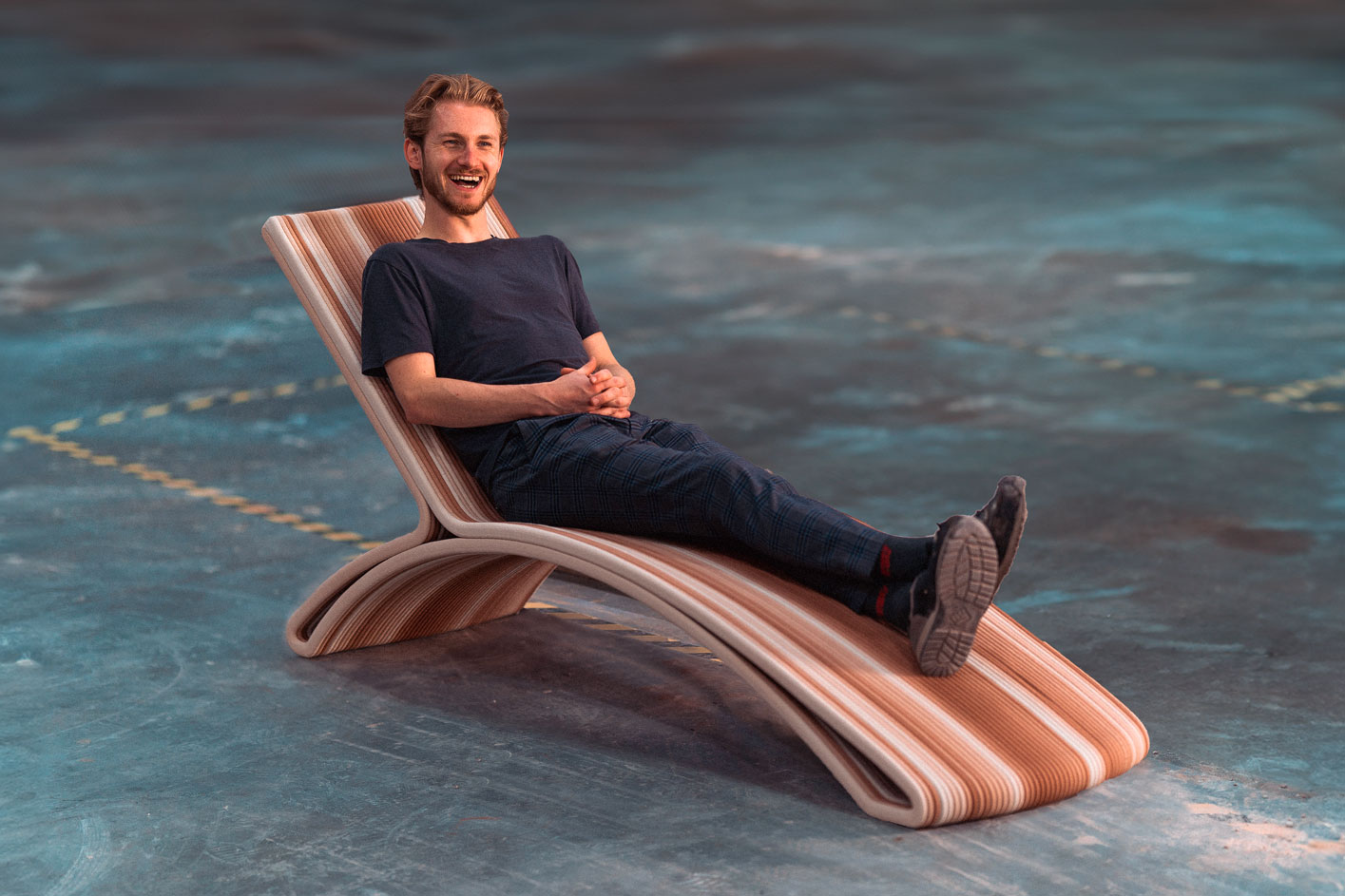
How Are Modular Furniture and Structures Revolutionizing Public Spaces?
Vertico is also proud to have worked on large public space projects. One of our notable projects is a parametric bench designed for the Tanthof Children’s Farm Foundation in Delft. This curved, over 20-meter-long bench serves as seating and edging for a large sand play area for toddlers.
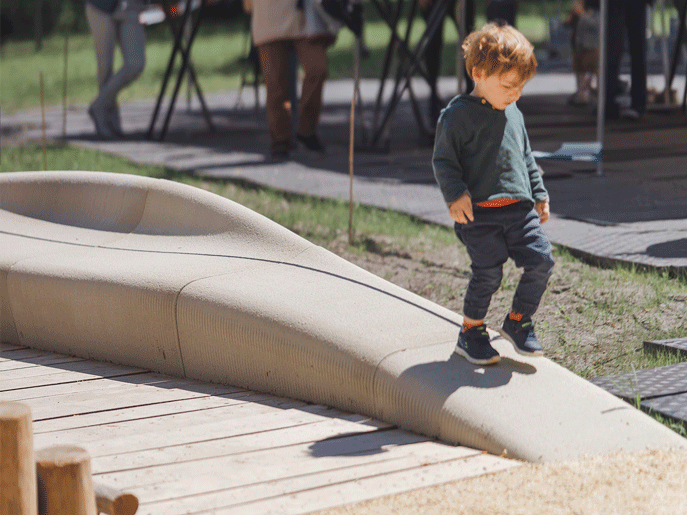
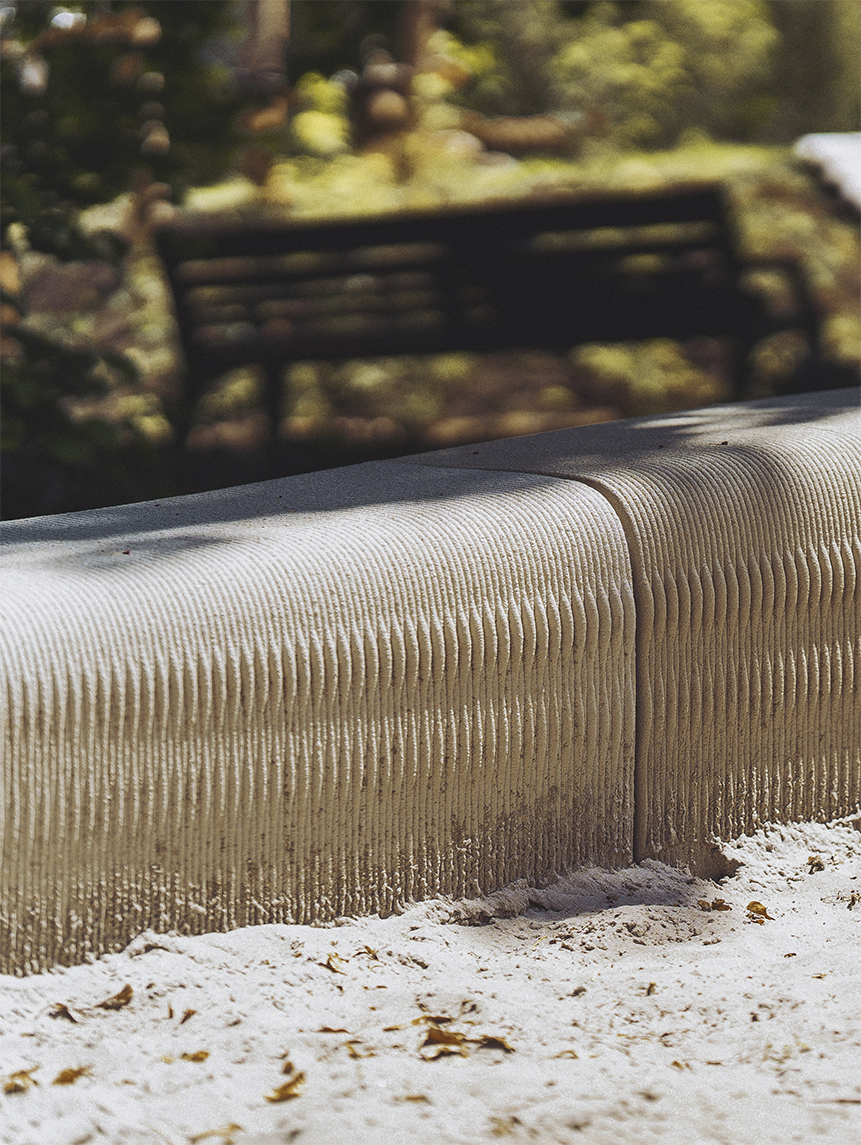
What makes this project special?
- Inclusivity: 3D printing enabled the creation of varied seating heights, ensuring comfort for everyone, from children to grandparents. Unlike traditional methods, this design decision didn't increase production costs.
- Material Reduction: The bench was designed as a hollow structure, reducing material use by 75%, making it both eco-friendly and cost-effective
- Formwork Elimination: No formwork was used in the creation of the bench, further reducing waste and resource consumption.
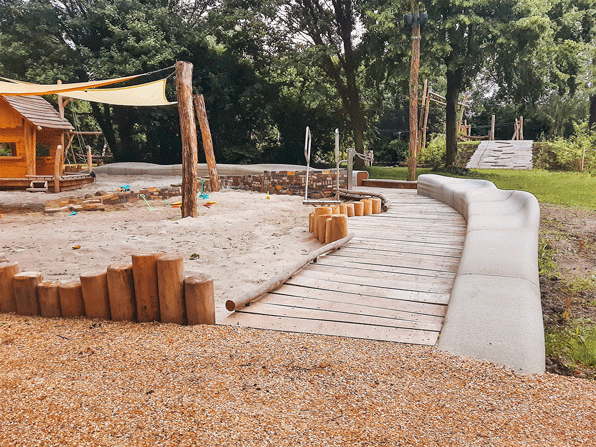
We’re excited to contribute to this fun and sustainable playground space, with future plans to optimize the material for even lower cement content, further reducing environmental impact.
Another notable project is the organized plant space in an office building, a prime example of modular urban furniture. This project, in collaboration with Heilijgers, demonstrates the versatility of 3D printed urban furniture, blending seamlessly with modern architecture while offering endless design variations.
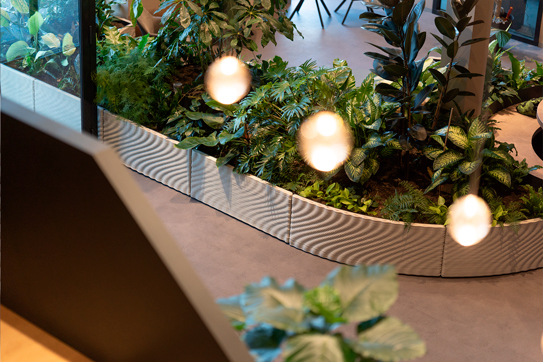
How Does 3D Printed Urban Furniture Contribute to Sustainable and Adaptable Spaces?
The ability to create customizable, sustainable, and adaptable furniture for public spaces is what sets 3D printed urban furniture apart. Whether it’s in playgrounds, office buildings, or outdoor spaces, 3D concrete printing offers a unique way to transform urban landscapes, making them more functional, eco-friendly, and visually appealing.