Parametric Design in Modeling
This summer, Vertico collaborated with IsolaGroup, a company specializing in exhibition design, to create a display space for one of the pavilions at the prestigious Dutch Design Week. Using parametric design and 3D concrete printing, we crafted custom pedestals that seamlessly blended form and function. Discover more about our project here: Pedestals for DDW Exhibition.
The Challenge:
The objective was to craft 15 pedestals that varied in height and size. These pedestals needed to:
- Enhance the displayed works of artists and craftsmen.
- Maintain a cohesive visual style across varying designs.
- Avoid drawing attention to themselves while highlighting the exhibits.
The Solution:
Using parametric design, our team developed a flexible and efficient modeling process. This approach allowed us to dynamically adjust each pedestal's geometry to meet specific requirements without compromising the overall design harmony.
What is parametric design?
Parametric design is a modeling process that allows the geometry of a model tochange dynamically when its dimensions or parameters are modified.
This is how parametric design works. Youstart with simple steps and slowly develop an algorithm.
We modeled everything in Grasshopper, a visualprogramming environment integrated with Rhino. In this specific project, we started by defining changing parameters, like height and a top radius (Figure A), followed by creatingpolygons (Figure B) and scaling them (Figure C), which could also be adjusted.
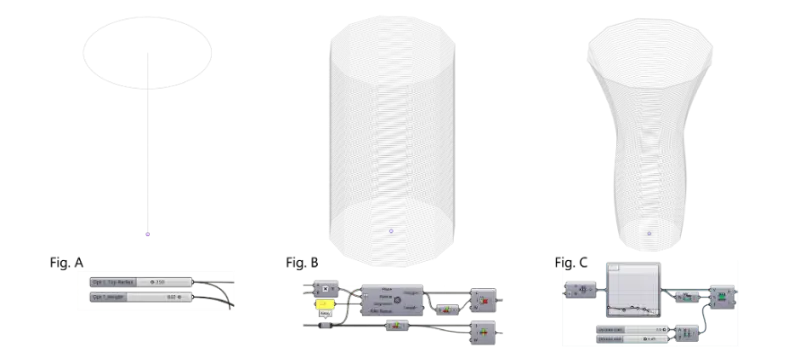
By changing the intensity of rotation (Figure D) we create a different texture for each of the pedestals. The result was an algorithm that could generate distinct objects based on specific parameters, yet all the pedestals clearly belonged to the same collection.
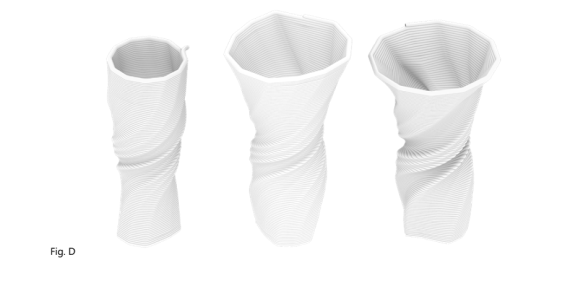
This flexibility exemplifies the power of parametric design: while initial time is spent developing the code, it pays offnby making later adjustments seamless. With just a few tweaks, we could adapt the design to meet specific requirements and optimize the production process.
About the Design:
The choice of white for the pedestals was deliberate. This neutral color ensured that the focus stayed on the artworks, not the stands. The goal was to create a smooth, fluid aesthetic, making the concrete appear almost soft and pliable, defying its traditionally rigid nature. This interplay between form and material highlights the innovative potential of modern technology.
About the Process:
Grasshopper, the visual programming tool, was the cornerstone of our workflow. It enabled us to:
- Rapidly iterate on designs.
- Experiment with varying parameters and textures.
- Ensure the pedestals maintained a consistent aesthetic while meeting the practical needs of the exhibition
This project was an exciting opportunity to combine parametric modeling and cutting-edge concrete printing techniques.