Gantry systems are large, fixed-frame 3D printers that move along three linear axes (X, Y, Z)—similar to CNC machines. These systems are designed for precision layering, making them ideal for large-scale, repetitive construction projects.
Best For:
- Printing large, uniform structures (e.g., houses and large walls).
- Companies aiming for fast, repetitive construction.
- On-site 3D printing for mass production of buildings.
Advantages of Gantry Systems
✔️ Scalability : Easily prints entire walls and structures in one setup.
✔️ Repeatability: Ensures consistent results for large, simple designs.
✔️ Lower Per-Unit Cost: If producing thousands of identical structures, costs go down.
Disadvantages of Gantry Systems
❌ Limited Design Flexibility: Can only print straight vertical layers; curves and angles are difficult.
❌ High Initial Costs: Requires significant capital investment ($200,000+ for a high-end system).
❌ Bulky & Non-Mobile: Requires dedicated space and is difficult to move.
Gantry systems are an excellent choice for companies looking to mass-produce housing and large concrete structures, but they lack the design flexibility needed for intricate, artistic, or highly customized architectural elements.
Robotic arms are multi-axis industrial robots that extrude concrete in a freeform manner, enabling greater design flexibility.
Best For:
- Architectural facades, sculptures, furniture, and intricate designs.
- Projects requiring complex curves, overhangs, and parametric forms.
- Small to medium-scale 3D printing applications.
Advantages of Robotic Arms
✔️ Extreme Design Freedom: Prints curves, angles, and organic forms with ease.
✔️ Compact & Portable: Takes up less space and can be moved between projects.
✔️ Lower Initial Cost: Entry-level robotic systems cost ~$50,000+, making them more accessible.
✔️ High Precision: Can create thin, detailed layers for artistic and architectural applications.
Disadvantages of Robotic Arms
❌ Limited Print Size : A single robot arm has a reach limit (~3m radius).
❌ Slower for Large Projects: Not ideal for printing full buildings unless using multiple robots.
❌ Requires More Programming Expertise : Needs customized toolpaths for complex designs.
Robotic arms are ideal for intricate, design-driven projects that require precision and flexibility, making them a strong choice for architects, designers, and innovators looking to push the boundaries of 3D concrete printing.
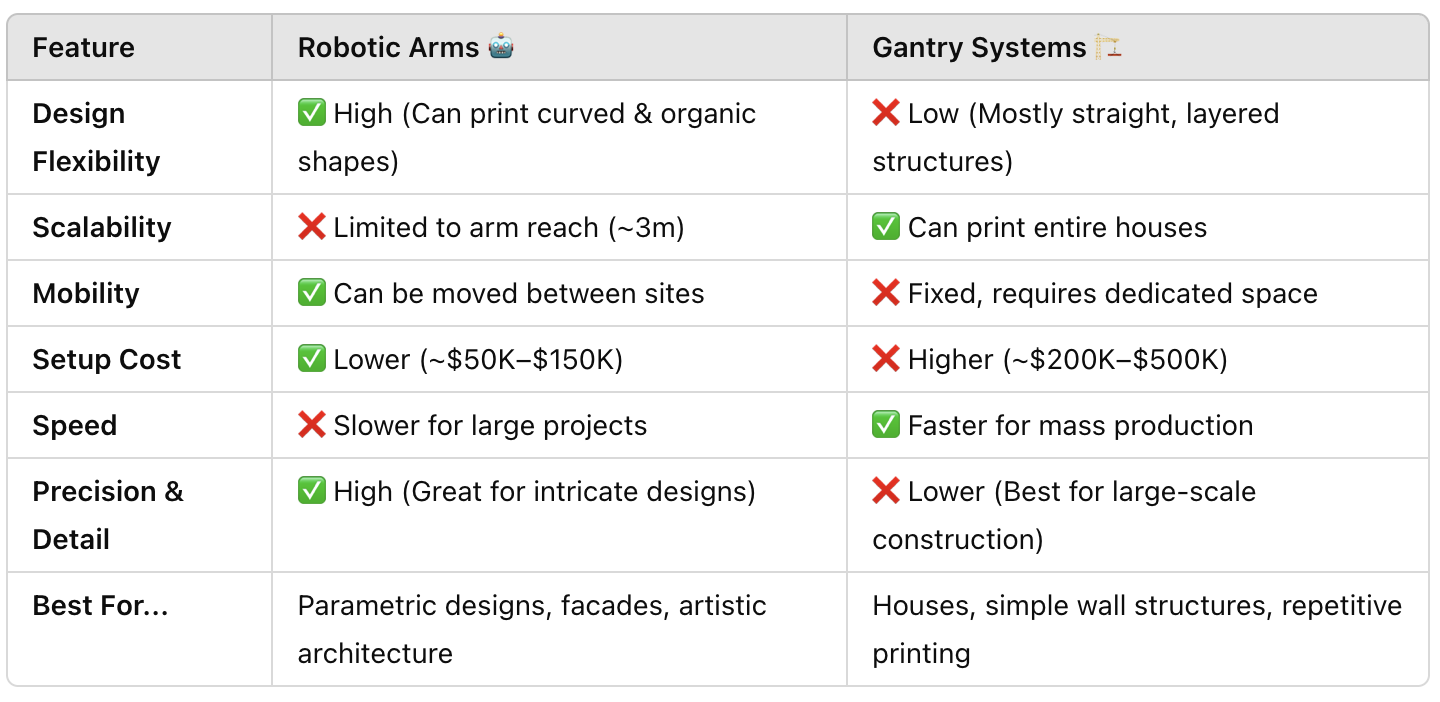
Why Vertico Chose Robotic Arms Over Gantries
1. Focus on Parametric & Architectural Applications
- Gantries limit creativity, while robots allow for freeform, parametric design.
- Vertico partners with architects and designers, rather than just construction firms.
2. Ability to Print Complex Overhangs (K2 Accelerated Printing)
- Most 3D concrete printers can only print 5-10° overhangs.
- Vertico’s robots (with K2 printing) can print up to 60° overhangs!
3. Lower Costs & Higher Flexibility
- Gantry systems are expensive and immobile.
- Robots allow modular, scalable printing setups without massive upfront costs.
4. Future-Proofing for Emerging Applications
- 3D printing is evolving rapidly. Robotics offers adaptability for facades, furniture, and future construction innovations.
See Robotic Arms in Action
Want to see the real potential of robotic arms in architectural concrete printing? Check out these innovative projects by Vertico:
Park Bench – A stunning example of organic, freeform design, only possible with robotic 3D printing.
Sand Mould Facades – Showcasing intricate, parametric facades that push the boundaries of architectural aesthetics.
Printing with Color – Exploring color integration in concrete printing, proving that robotic arms can go beyond structure and into artistic expression.
The Future: Will Robots and Gantries Work Together?
While robots dominate in creativity and gantries lead in mass production, there’s potential for hybrid systems:
- Using robots for intricate facade panels, then assembling them into buildings.
- Combining gantries with robotic arms for more complex structures.
As the industry evolves, the biggest breakthroughs may come from integrating the best of both worlds
Choosing between robotic arms and gantry systems comes down to your project needs. If you require large-scale, repetitive construction, see how 3D printing is being applied in construction. However, if you're looking for unmatched design freedom, precision, and flexibility, explore innovative architectural applications of robotic 3D printing.